Ongoing Sale, 2010 Pulp Tray Molding Line
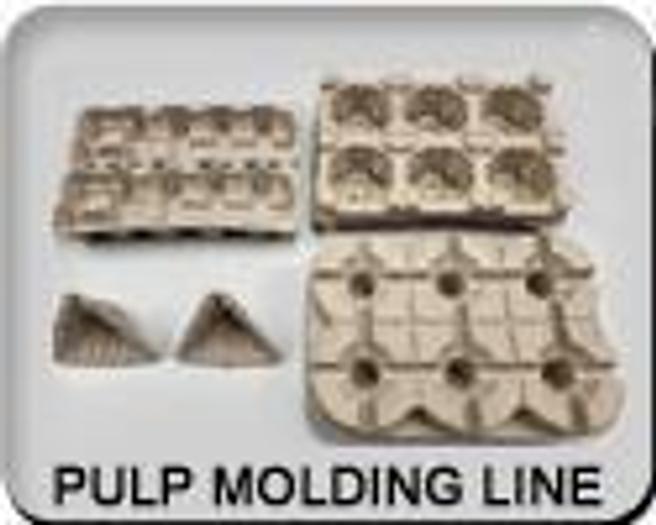
Information
Private Negotiation Sale - Available For Immediate Sale
2010 Pulp Tray Molding Line
Fulfilling Customer Requests; The line can be engineered to provide protective molded pulp trays of different designs and geometries for a wide variety of products, from electronics to candles, consumables and more. The line is fully integrated processing paper substrates to pulp slurry continuous to thermoforming unlimited tray type shapes, continuous through automated drying oven, with finished product discharged to stacking tables
PULP MOULDING SYSTEM-DRYER COMPONENTS
Machine: 16 ¼” x 60” moulder c/w process system
Dryer: Four pass one zone single burner dryer, Conveyor tray dryer, power source natural gas
Platen Size; 60" x 16"
Product Size: 4 x 14 ½” (58”) long x 14.5” wide x 6” high
Product Weight: 6 x 142 grams (.31 lbs) = 852 grams (1.87 lbs) per drop
Production Weight: 3.8 kg/8.36 lbs. per minute; 230 kg/506 lbs. per hour
Max Number of Drops: 4.5 drops per minute
Number of Pieces per Year: As per calculator
The molder is operated with a hydraulic drive for the transfer and the molding drum. The touch screen gives the operator complete control over all moulder automatic and manual functions.
Equipment Specifications
One Travaini 150 hp 1750 cfm vacuum pump for high vacuum, complete w/ base, motor and 44 gpm seal water system w/ cooling and automatic shut off
Two stainless steel vacuum separator tanks and (2) 200 gpm white water recovery pump system w/ automatic level control, valves & gauges
One air receiver and one air puff tank w/ inline filter, regulator, and lubricators
All necessary electrical controls and starters all wired to a control panel that can be run in automatic or manual
One stainless steel moulding vat w/ a constant flow system for product weight control, one 125 gpm pulp transfer pump 90-gallon stainless steel circulation tank
Four structural steel welded frame w/ a heavy epoxy coating
One hydraulically driven stainless steel moulding drum w/ quick die clamps for quick die change, anti-friction bearings and rotary actuator (Platen size 16 ¼” x 60”)
One Hydraulically driven stainless steel transfer w/ stainless steel die mounting bars
One 3500-gallon stainless-steel white-water tank w/ a 250 gpm transfer pump
One white water heat recovery system from the dryer exhaust cw 30 gpm cir. Pump
One 230 psi die and decal wash pump and spray wash gun for cleaning dies
One 25 HP 1000 psi hydraulic unit, cylinders, and drive motor for moulder
Two 60 HP pulper motor and 1450-gallon pulper c/w propeller
Two automatic paper pulper lifting bins
All process air, water and pulp pipes are stainless steel
Drying- Oven Components
Dryer BTU’s 2,500,000
One Maxon Ovenpak Burner, natural gas low NOX & Co @ 2.5 MBTU’s
Circulation Fan: Two New York plug fans Model 208 PLR @12,000 cfm
Exhaust fan: 4,000 to 6,000 cfm variable speed general purpose fan
The drying temp is set manually for the different products and is automatically controlled
The dryers have a high temperature cut off and E stops for safety reasons
The dryers are complete with a user-friendly PLC control panel
The fans will be complete w/ V-belt drives, guards, and electrical motors
The exhaust stack will be provided to exhaust fan and manufactured out of 24-gauge galvanized sheeting and will need to be installed and vented outside on site
The exhaust systems include a water recovery and white-water heating system
The exhaust has a heat transfer system to transfer heat energy from the exhaust air to the makeup air supply c/w 30 gpm transfer and 50 gallon holding tank
The dryer enclosures are manufactured out of standard 18 gauge galvanized and stain coat insulated panels
The panels are assembled to provide a sealed enclosure
One automatic stacker
One product packing table
This system has:
Stainless steel moulding drum and transfer face
Stainless steel moulding vat
Automatic die and decal wash system
Automatic transfer die oiling and cleaning system
Manual and automatic operating settings
Constant flow pulp recycling system
The matching dryer is built to equal the production rate of the moulder and is fabricated from structural steel and heavy galvanized steel sheeting. NOTE: Water is mostly recovered and reused IMPROVEMENTS /Replacements SINCE INSTALLATION IN 2010 March 2017 – New vacuum pump January 2019 – New vacuum pump motor 2021 – Dryer completely rebuilt: All new interior walls, insulation, roof, duct work, exhaust blowers, circulation blowers, gas fired burner, electrical, dryer trays, conveyor chains, chain tracks sprockets and shafts 2022 – Replaced both pulper shafts and bearings 2022 – New hydraulic rotary actuator and bearings One new spare seal water pump Two new spare pulp recirculation pumps
Equipment Location
North Haven, CT
USA
Inquiries Contact
Tom Gagliardi
tomjr@thomasauction.com
203-641-2216